welcome to usa fluid ends the united states most trusted name in fluid end products , sales & service
FLUID END MODELS
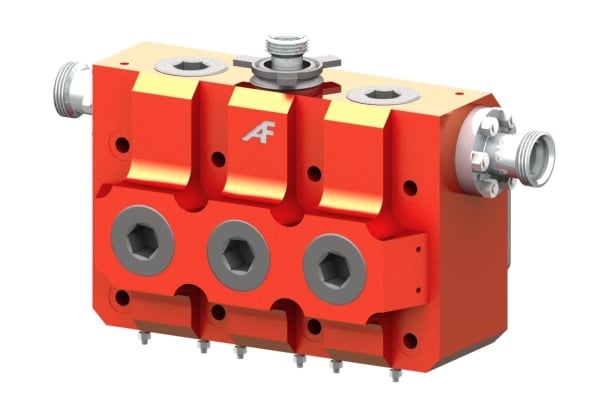
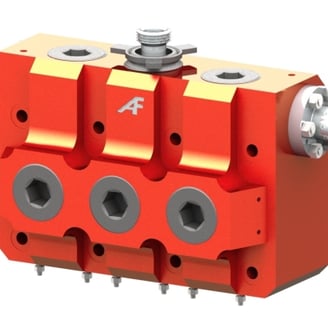
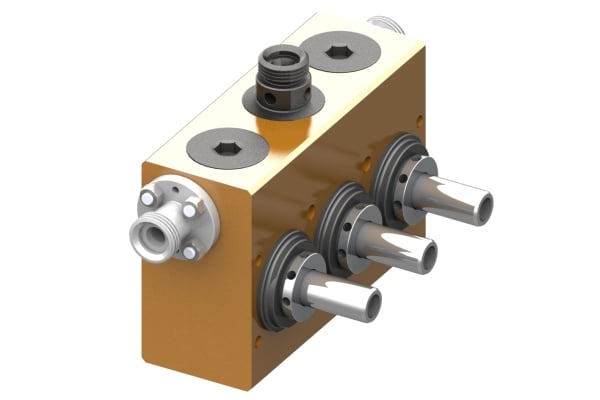
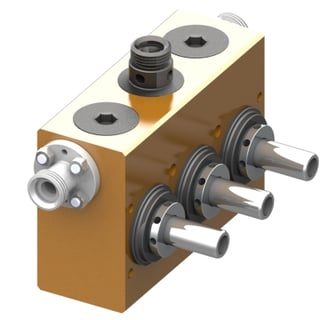

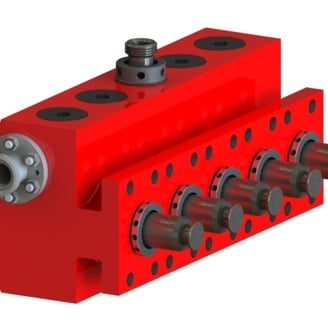
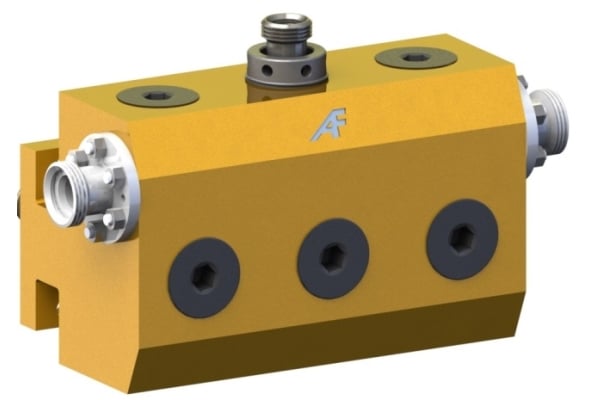
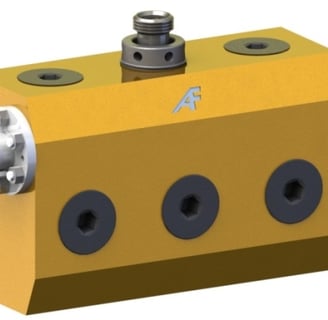
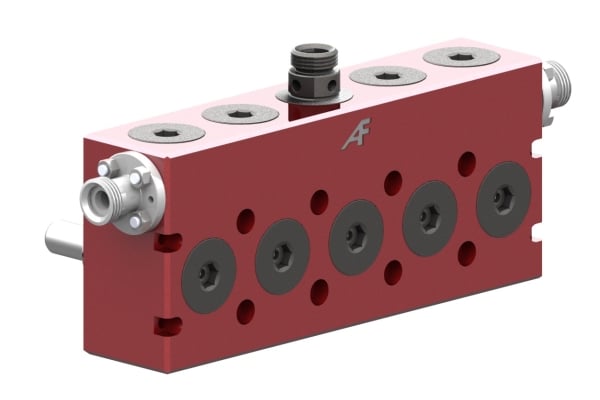
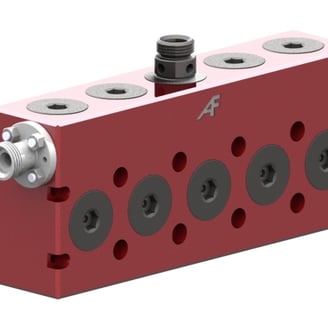
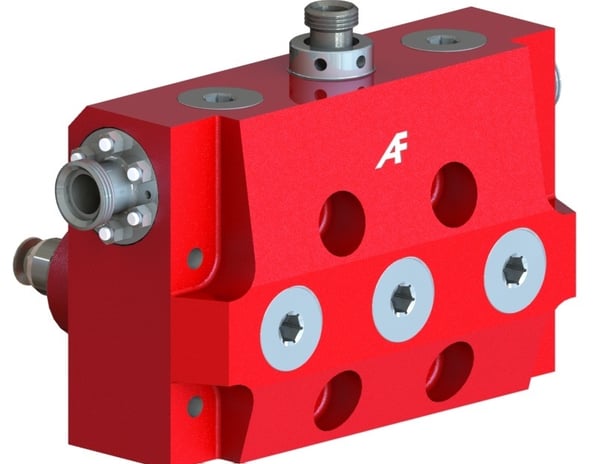
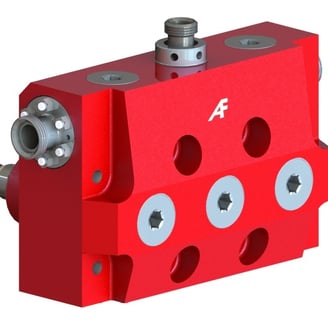
X Series
USA600 600HP Triplex, 6″ Stroke, 9″ Centers
USA1000 1000HP Quintuplex, 6″ Stroke, 9″ Centers
USA2250 2250HP Triplex, 8″ Stroke, 12″ Centers
USA2400 2400HP Triplex, 10″ Stroke (for FMC WT2400)
USA2500 2500HP Qunituplex, 8″ Stroke, 10″ Centers
USA2500 2500HP Quintuplex, 60″ Y Block, 8″ Stroke, 12″ Centers
USA2500 2500HP Triplex, 10″ Stroke (for SPM TWS2500)
XL – Series
USA2250XL 2250HP Triplex, 8″ Stroke, 12″ Centers
USA2400XL 2400 Triplex, 10” stroke (for FMC WT2400)
USA2500XL 2500HP Quintuplex, 8″ Stroke, 10″ and 12″ Centers
USA2500XL-DES 2500HP Triplex, 10″ Stroke w/ Integral Stuffing Box (for SPM TWS2500)
USA2700XL 2700 Quintuplex, 10” stroke (for *FMC WT2700)
PARTS
Main Fluid End Components:
Fluid End Block (Module) – The forged steel or alloy body that houses all the high-pressure components.
Discharge Module – The upper chamber where fluid exits the pump.
Suction Module – The lower chamber where fluid enters the pump.
Valve Seats – Hold the valves in place and provide a sealing surface.
Valves
Discharge Valve – Controls fluid outflow.
Suction Valve – Controls fluid inflow.
Valve Springs & Guides – Assist valve movement and alignment.
Liners (Sleeves) – Wear-resistant sleeves inside the cylinder bore.
Plungers or Pistons – Create the pressure by reciprocating inside the liners.
Pony Rods / Extension Rods – Connect the crosshead to the plunger/piston.
Packing (Packing Sets / Packing Cups) – Seals around the plunger to prevent fluid leakage.
Packing Glands / Packing Nut – Holds the packing in place.
Wear Plates / Retainer Rings – Provide liner support and seal integrity.
Cylinder Head Caps / End Caps – Close off ends of the fluid end and provide access for maintenance.
Crosshead Guide / Stuffing Box – Houses packing and connects to the power end.
FOR YOUR INFORMATION:
These are reciprocating positive displacement pumps, often referred to as frack pumps or well service pumps. They're used to inject high-pressure fluids into oil or gas wells for a variety of purposes, most notably hydraulic fracturing.
Terminology Explained:
Triplex / Quintuplex:
Refers to the number of plungers (pistons) in the pump:Triplex = 3 plungers
Quintuplex = 5 plungers
More plungers generally mean smoother flow and higher capacity.
Stroke:
The linear distance the plunger travels inside the pump—e.g., 6", 8", 10". Longer strokes generally allow for more fluid per cycle.Centers:
Distance between the centers of each plunger cylinder. Impacts pump size and internal geometry.HP (Horsepower):
Indicates the power rating of the pump. Higher HP = ability to pump at higher pressures or volumes.Y Block / Integral Stuffing Box:
These are design variants in the fluid end of the pump. The Y Block is a specific shape/configuration, and integral stuffing box means it's built into the fluid end for sealing around the plunger.FMC, SPM:
These are OEM (original equipment manufacturer) references. Your pumps are described as equivalents or replacements for pumps made by companies like FMC or SPM, which are major suppliers in this space.
Typical Uses:
Hydraulic fracturing (fracking): Injecting high-pressure fluid into rock formations to release oil or gas.
Well stimulation: Enhancing oil/gas recovery from existing wells.
Cementing or acidizing operations in well services.
MICHAEL DEAN PIERCE JR. SALES REP
832-474-4440
CALL OR TEXT 24/7
★★★★★
Predict the future by creating it
USA Series Pump Model Reference Chart
ModelHP Type. Stroke. Centers. Notes / EquivalentUSA600600Triplex6″9″Legacy SeriesUSA10001000Quintuplex6″9″Legacy SeriesUSA22502250Triplex8″12″Legacy SeriesUSA24002400Triplex10″—For FMC WT2400USA25002500Quintuplex8″10″Legacy SeriesUSA25002500Quintuplex8″12″ (Y Block)60″ Y BlockUSA25002500Triplex10″—For SPM TWS2500
USA XL Series Pump Model Reference Chart
Model HP. Type. Stroke. Centers. Notes / EquivalentUSA2250XL2250Triplex8″12″AFE XL SeriesUSA2400XL2400Triplex10″—For FMC WT2400USA2500XL2500Quintuplex8″10″ and 12″AFE XL SeriesUSA2500XL-DES2500Triplex10″—Integral Stuffing Box, for SPM TWS2500USA2700XL2700Quintuplex10″—For *FMC WT27
LEARNING IS POWER
History of High-Horsepower Reciprocating Pumps in Oil and Gas
The evolution of high-horsepower reciprocating pumps in the oil and gas industry has played a crucial role in transforming drilling, production, and well services. From the early days of oil extraction to the modern hydraulic fracturing (fracking) processes used to unlock shale oil and gas reserves, these pumps have been at the forefront of ensuring high-pressure fluid injection to stimulate and enhance oil and gas production.
Early Beginnings: The Birth of Reciprocating Pumps
The story of reciprocating pumps in the oil and gas industry begins in the 19th century, when the first crude oil wells were drilled. Pump technology was required to lift oil from underground reservoirs to the surface. The earliest pumps were manual or steam-powered and used basic piston-driven mechanisms to move fluid.
In the early 1900s, triplex pumps (three plungers) were developed and became the standard in the industry. These pumps allowed for smoother and more reliable pumping action, essential for extracting oil from increasingly deeper wells.
The Rise of High-Horsepower Pumps in the Mid-20th Century
As the oil and gas industry grew, so did the demands for more powerful equipment to handle greater pressure and higher flow rates. The development of high-horsepower pumps became critical to meeting these new challenges, especially as exploration moved into more remote or difficult-to-reach areas like the deep offshore, oil sands, and shale formations.
By the 1950s and 1960s, high-horsepower triplex pumps were already a common feature in many oilfields. These pumps could handle up to 2,000-3,000 horsepower (HP), powering larger hydraulic systems and improving operational efficiency. The advent of quintuplex pumps (five plungers) soon followed to provide even higher capacities and smoother, more consistent pumping action, ideal for high-demand applications.
The Birth of Hydraulic Fracturing and Well Stimulation (1970s-1980s)
The 1970s and 1980s marked a pivotal period in the history of well service pumps, driven largely by the rise of hydraulic fracturing (fracking). This revolutionary technique involved injecting high-pressure fluid into the wellbore to fracture underground rock formations, allowing oil and gas to flow more freely to the surface.
As fracking operations expanded, so did the need for high-pressure, high-flow pumps that could handle the extreme demands of the process. Pumps like the triplex and quintuplex designs were re-engineered to withstand the high pressures (often exceeding 10,000 psi) required to fracture the rock formations. The introduction of USA-made pumps, including the AF series and AFE XL series, represented a significant milestone in the development of pumps specifically designed for hydraulic fracturing.
Technological Advancements and Modern High-Horsepower Pumps (1990s-Present)
The last few decades have seen significant technological advancements in the design and performance of reciprocating pumps. Innovations such as integral stuffing boxes, advanced sealing technologies, and electronic monitoring systemshave improved the performance, reliability, and efficiency of high-horsepower pumps. Manufacturers began to focus on creating pumps capable of 10,000 psi or higher operating pressure, required for fracking operations in deep shale formations.
Additionally, environmental concerns have driven the development of pumps with lower emissions and more energy-efficient systems. These USA-made pumps are built with precision engineering to meet increasingly strict regulatory standards while maintaining their rugged performance in demanding oilfield operations.
Today, high-horsepower pumps like the USA2250, USA2500, and USA2700XL offer a combination of power, durability, and efficiency, supporting a wide range of applications from fracking and cementing to acidizing and well stimulation. Their Triplex and Quintuplex designs remain the standard for the oil and gas industry, with many pumps now able to operate in the harshest environments with minimal downtime.
The Future of High-Horsepower Pumps
As the demand for oil and gas continues to evolve, so too will the need for more powerful, efficient, and reliable pump solutions. The future of high-horsepower pumps is likely to be driven by continued innovations in materials science, automation, and smart technologies. These advancements may lead to even more durable and energy-efficient pumps, capable of operating at even higher pressures and with greater environmental responsibility.
At the same time, the trend toward shale gas exploration and unconventional resource extraction will continue to push the limits of pump technology. Sustainable fracking methods, along with advances in pump designs, will shape the future of high-horsepower pumps in the oil and gas industry for years to come.
Key Milestones in Pump History:
1900s: The birth of triplex pumps for oil extraction.
1950s-1960s: High-horsepower triplex pumps are introduced to meet the needs of deeper and larger oilfields.
1970s-1980s: The development of pumps for hydraulic fracturing coincides with the growth of well stimulation technologies.
1990s-Present: High-tech advancements, including the introduction of AFE XL Series and integral stuffing box designs, as well as a focus on environmentally friendly technologies.
Future: Continued development of energy-efficient, higher-pressure pumps for deeper, more challenging wells.
The History of Fluid Ends in High-Horsepower Pumps
Fluid ends are integral parts of reciprocating pumps, particularly in oilfield services like hydraulic fracturing (fracking) and well stimulation. These components are responsible for directing and controlling the flow of fluids under high pressure, and their design has evolved significantly over the years to handle the increased demands of modern oil and gas operations.
Early Development and Pioneering Fluid End Designs (Late 1800s - Early 1900s)
The origin of the fluid end dates back to the early days of piston pumps used in the oil industry. In the late 1800s to early 1900s, as oil production began to take off, the need for more reliable positive displacement pumps grew. These early pumps, often driven by steam engines or manual labor, used simple piston-driven designs that had a fluid end housing a single piston or plunger.
At this time, fluid ends were rudimentary, designed to handle the basic task of pumping oil or water from underground reservoirs. However, the need for more durable and efficient designs became apparent as the oil industry expanded and deeper, more challenging wells were drilled.
The Introduction of Triplex Pumps and Fluid End Advancements (1930s-1950s)
By the 1930s and 1940s, the introduction of triplex pumps (pumps with three plungers) in the oil industry significantly changed the way fluid ends were designed. This new design allowed for smoother, more consistent pumping action, providing greater efficiency and reliability.
As the demand for more powerful equipment grew, the fluid ends also had to evolve. Fluid ends were now being engineered to handle higher pressures and increased flow rates, essential for extracting oil from deeper wells. The material composition of the fluid ends improved as manufacturers began using high-strength steels and alloys that could better withstand the harsh environments of oilfields. This led to the development of the first triplex fluid ends, designed to handle the multiple plunger configurations typical in these pumps.
The Rise of Hydraulic Fracturing and Fluid End Design (1970s-1980s)
The 1970s and 1980s were a transformative period in the history of fluid ends, largely driven by the rise of hydraulic fracturing (fracking). The introduction of high-pressure fracturing techniques in oil and gas extraction demanded pumps capable of handling extreme pressures and challenging environments. Fluid ends had to be reinforced to deal with the high-pressure injections of fluid required to fracture rock formations deep underground.
During this time, manufacturers focused on improving the durability and efficiency of fluid ends. Key innovations included:
Stronger, more durable materials (such as forged steel and chromium alloys) that could withstand the pressure and abrasive nature of fracturing fluids.
The development of advanced sealing systems to prevent fluid leakage under extreme pressures.
Interchangeable fluid end components, allowing for easier maintenance and repairs in the field.
One of the major advancements during this period was the development of the “stuffing box” design, a component that helped seal the area around the plunger to prevent fluid leakage, which was especially critical in high-pressure fracking operations. The stuffing box kept the pump seals intact, ensuring reliability and reducing downtime.
The AFE Fluid End Revolution (1990s - Early 2000s)
As hydraulic fracturing became more widespread in the 1990s, the demand for high-performance fluid ends grew significantly. Pump manufacturers, including companies like SPM, FMC, and USA Pump Manufacturers, began developing AFE fluid ends (AFE standing for "Advanced Fluid End"). These designs incorporated the latest materials and engineering practices to meet the increasingly demanding conditions of fracking operations.
Some of the key innovations in AFE fluid ends during this period included:
Integral Stuffing Boxes: These eliminated the need for separate sealing components and provided greater reliability by ensuring better containment of fluid pressures.
Modular Designs: This allowed for easier maintenance and fewer parts replacements, reducing overall operating costs.
Advanced Coatings and Surface Treatments: Fluid ends were coated with specialized materials like chrome plating or ceramic coatings to resist the abrasive nature of fracking fluids, which often contain sand and other particulates.
Increased Pressure Ratings: Fluid ends began to be engineered to handle higher pressures (up to 15,000 psi and beyond), meeting the growing needs of deeper and more complex shale formations.
Modern Fluid End Designs (2010s - Present)
Today, fluid end technology continues to evolve to meet the ever-increasing demands of modern oil and gas operations. Fluid ends are now being designed to handle extreme pressures (up to 20,000 psi or higher) and are built to last even in the most challenging environments.
Some of the latest innovations in fluid end design include:
Advanced Composite Materials: Fluid ends are now being constructed with lightweight yet durable composite materials that resist wear and tear, allowing for longer service intervals.
Digital Monitoring Systems: Modern fluid ends are equipped with sensors and IoT technology to monitor performance in real-time, providing valuable data for predictive maintenance and reducing downtime.
Enhanced Sealing Systems: New sealing technologies, such as dynamic sealing solutions, ensure that fluid ends can handle higher pressures and provide a longer lifespan between repairs.
Customizable Fluid Ends: Manufacturers offer customized solutions to meet specific requirements, such as special coatings or designs for unique fracking operations, enabling pumps to operate efficiently in a wider range of conditions.
The Future of Fluid Ends
The future of fluid ends in the oil and gas industry is poised to focus on sustainability, automation, and efficiency. As the industry continues to push the boundaries of what is possible in terms of depth, pressure, and resource extraction, fluid ends will continue to evolve. We can expect further advancements in materials science, such as the development of even more wear-resistant alloys, as well as smart fluid end systems that use real-time data to optimize pump performance and reduce environmental impact.
Key Milestones in Fluid End History:
Late 1800s to Early 1900s: Basic piston-driven fluid ends for early oil extraction.
1930s-1950s: Development of triplex fluid ends to handle higher pressures and flow rates.
1970s-1980s: Hydraulic fracturing drives the need for high-pressure fluid ends, leading to the creation of stuffing boxes and reinforced designs.
1990s-2000s: Introduction of AFE fluid ends, modular designs, and high-pressure capabilities.
2010s-Present: Integration of advanced materials, digital monitoring, and customization for specific applications in modern well service operations.
Location:
USA FLUID ENDS
13840 ASTON RD SUITE A
HOUSTON TX 77040
contact:
TEXT, CALL
832-474-4440
© 2025. All rights reserved.